SERIE 6000
HYBRID COMBINED CYCLE
Capacity: 33 to 300 tons
(99 to 900 GPM @ 95°F/85°F/78°F)
- Available in galvanized, galvanized with
epoxy coating for marine environments
and stainless steel - Low installation and operating costs
- Little noise and vibration
- Low power consumption per ton
- Easy maintenance
- Automated variable capacity system
by a programmable control panel
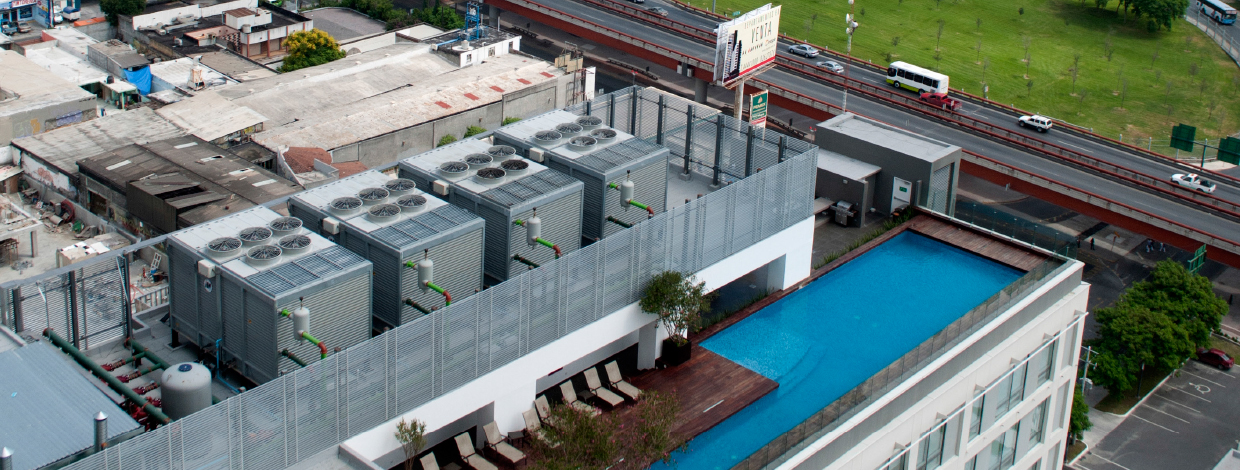

SERIES 6000 ADVANTAGES


Rotating-turbine nozzles vs. fixed-orifice stationary nozzles
The rotating-turbine (A) variable-flow sprinklers used for IM® towers provide a square, constant and uniform distribution pattern, irrespective of the flow of processed water.
Fixed orifice stationary sprinklers (B) provide uneven, conical dispersion patterns that create dry areas and water overload areas, which may change in response to variations in flow.

Twin wall
The interior flat wall in the packing area reduces “loss through the wall”, thereby increasing tower efficiency.

High-efficiency PVC laminate packing
Supported on the floor, with integrated drip and entrainment removers, which may be replaced without having to disassemble the tower.

Low sound and vibration level
Independent, pressurized ventilation systems with high-efficiency and low-noise level FRP axle ventilators directly connected to low-speed TEFC electric motors.

Self-supporting structure
Hybrid structure (steel/FRP) does not need to be disassembled on a support beam structure, thus saving on installation costs.

Pumping system
Independent cooling water pumping systems integrated into the machine.


Sistema de serpentín
“Hung” on side rails and fluid connections in distributor heads. Configuration allows easy and quick extraction of the coil assembly for maintenance purposes. Assembly in models of the same group allows changing the size of the coil so as to increase or reduce machine capacity. Available in hot-galvanized steel or 304 or 316 stainless steel, both of which meet ASME B31.5 specifications. True parallel air/water flow on the coil, which eliminates dry areas and allows operation at a greater volume of air and water, without any increase in the system static pressure. At the same time it creates a ‘washing’ effect that prevents the formation of incrustation on the outer surface.


The modular ventilation system
The modular ventilation system has the facility to configure each section of the machine with 1, 2 or 3 ventilation modules, as needed to achieve the capacity required or to increase the capacity of an existing machine.
Variable-Capacity Automatic
Control System
The tower has the facility to be integrated into a system so as to operate at maximum efficiency. The system automatically detects failure of any system component and takes automatic action to change the equipment to the right failure operating mode.
The intelligent control software, completely developed by IM®, provides users
the facility to enter all control parame- ters so that the
machine may operate fully automatically at the highest possible
level of operating stability and energy efficiency.
All data are directly entered onto the terminal screen and the system
may also be connected to a central console or a
computer via Ethernet or TCP/IP.
The Control System includes all logical control and power
components required to operate all cooling tower elements and
the process fluid pumping system.


he touch control terminal (HMI) may be found on the front of the panel, together with all components for controlling the system in automatic, semiautomatic or manual mode in the event of PLC failure.
Operating Modes
The twin-section configuration of the IM6000 is unique in the industry and allows the machine to operate at greater process fluid outlet temperature stability. This tower is very versatile, as it may operate in several modes and at several capacity stages within each operating mode, thereby achieving high levels of energy efficiency, reducing use of evaporation water, thus substantially reducing operating costs.

Air only (variable flow) on the coil
Sensitive cooling/cooling water not used.

Air (variable flow) and water (fixed flow) on the coil
Indirect latent cooling / Uses some evaporation water.

Air (variable flow) and water (fixed flow) on coil and packing
Indirect latent cooling and hybrid cooling (sensitivelatent),
with no air induction.

Water (fixed flow) on the coil and packing, and air
(variable flow) on packing
Direct sensitive cooling and direct latent cooling
(evaporative) with induced air on packing

Air (variable flow) and water (fixed flow) on the coil and packing
Indirect latent cooling (evaporative) and direct
latent cooling (evaporative) wit induced air.
Why hybrid? See More
IM® 6000 towers use both thermal exchange processes: sensitive and latent. They may also operate with just air in the outer part of the coil, so the cooler operates at 100% sensitive cooling and does not use evaporation water.

Sensitive Cooling
This is produced by the thermal exchange between hot liquid and cold liquid, without
there being a change in mass from one liquid to another.
When cooling hot liquid in indirect contact with a mass of moving gas, an interchange
takes place by convection due to the difference in temperature between the mass of the
liquid and the temperature of the gas. As there is no exchange of mass, there is no evaporation
of a part of the liquid, nor is there any increase in the relativity humidity of the mass of gas.

Latent Cooling (Evaporative)
This is produced by a simultaneous thermal/mass exchange that uses the energy required to
evaporate hot liquid (latent evaporation heat) and the difference of heat content between the
liquid and gas as the main motor of the cooling process.
Single cycle VS. Hybrid combined cycle See More
Single Cycle
LOW ENERGY EFFICIENCY
1 The process fluid circulates within the coil and the cooling fluid, together with the airflow, circulates outside the coil.
All thermal energy to be dissipated passes from the processing fluid to the cooling fluid through the wall of the coil.
2 All thermal energy gained by the cooling fluid when passing outside the coil has to be dissipated into the atmosphere so that cooling fluid falls on the lower cooler tray at the same temperature as that at which it was originally sprayed on the coil.
System requirements: A high-power ventilation system that has the facility to move a large mass of air in a high-pressure drop ventilation system with which energy efficiency is very low, particularly when the systems operate at a wet-bulb temperature over 65°F or approaches close to 14°F.
Hybrid Combined Cycle
ENERGY EFFICIENCY
Two thermal dissipation sections, one primary made up
of the single cycle as described above, plus a secondary
dissipation section.
3 Made up of a direct evaporative
exchange system in which the remaining thermal energy
is dissipated into the atmosphere before cooling water is
returned to the upper part of the primary section
4 System requirements: A much lower power ventilation system, as its aerodynamic system is much more efficient. This means its energy efficiency is much greater than the single system, in particular when operating at a wet-bulb temperature of more than 74°F or with approaches of less than 12°F.

The energy consumption of the single cycle is more than 200% of that required by the combined-cycle system.
Do you have doubts or would you like
Know more about the 6000 Series?
Let’s talk
In Mexico: 800 263 5300
Other countries: +52 (81) 1158-5300
Are you ready for
quote?
Please fill in the form data
And we will get in touch with you
To give you the quote.